Ti-6Al-4V (Ti-64) is considered the workhorse titanium alloy, accounting for over 50% of titanium use globally. Originally developed for the aerospace industry, Ti-64 has seen widespread adoption in the energy and biomedical fields due to its high strength-to-weight ratio, excellent corrosion resistance, and outstanding biocompatibility.
Within the aerospace and energy sectors, Ti-64 components are exposed to extreme operating conditions, where service temperatures can reach 400 °C. One example of such conditions is found in gas turbine engines, where Ti-64 is utilized extensively. To accurately design and validate parts for these high-stress applications, it is critical to understand the mechanical properties of Ti-64 at elevated temperatures.
Sample Preparation and Testing Procedure
To collect reliable mechanical data, samples were precision-machined from bar stock on our HAAS TL1 CNC Lathe to meet ASTM E8 specifications. Two thermocouples were attached to the surface of each sample and were carefully shielded from direct heating to ensure accurate and uniform temperature during the test.
The prepared samples were loaded into an MTS 810 tensile testing frame equipped with water-cooled grips and a high-temperature furnace. Tensile tests were conducted at 200 °C, 400 °C, and 600 °C. Prior to testing, each sample was soaked under zero load for a minimum of 20 minutes to allow the temperature to fully stabilize throughout the material before applying a uniaxial tensile load. All tests were conducted in accordance with ASTM E21.
Material Behavior at Elevated Temperatures
Mechanical properties of a material can vary significantly depending on the service environment. Typically, as temperature increases, the overall strength decreases while ductility (or elongation to failure) increases. These trends are influenced by the thermal stability of the alloy’s microstructure.
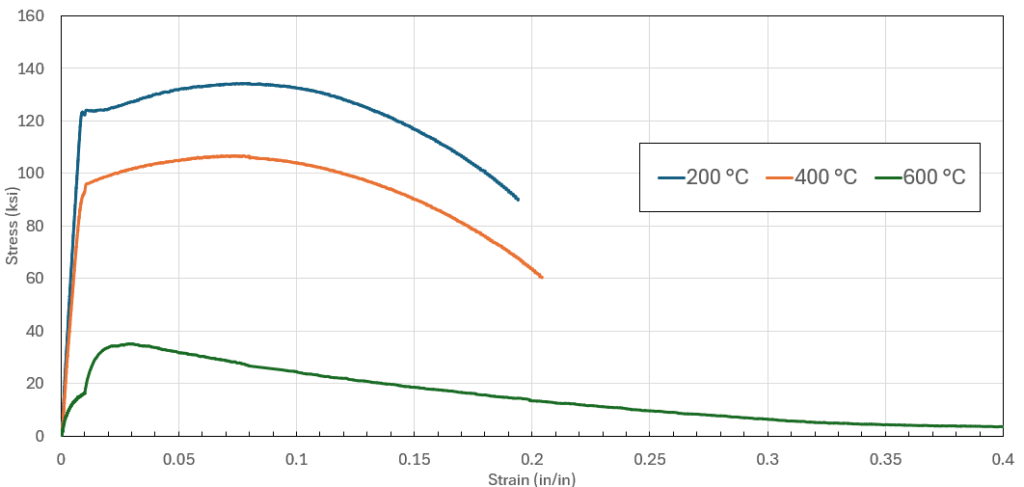
Figure 3: Stress-strain curves depicting the different tested temperatures.
At elevated temperatures, phase transformations or precipitate dissolution may occur, leading to noticeable changes in mechanical behavior. For Ti-64, this becomes particularly relevant above 980°C, which is the material’s β-transus temperature. However, for service conditions, the practical upper limit for Ti-64 is around 400 °C, as strength begins to drop beyond this point — a trend clearly observed in this testing.
The results underscore the critical need for elevated temperature tensile testing when designing components intended for high-temperature applications. Without accurate temperature-dependent data, there is a risk of underestimating material behavior, leading to potential performance issues in service environments like gas turbines or energy generation systems.
Need Reliable High-Temperature Tensile Data?
Secat, Inc. offers precision mechanical testing services for titanium alloys, including Ti-6Al-4V. Our capabilities include elevated temperature tensile testing, fatigue and fracture testing, and a deep understanding of the relationships between microstructure and performance for aerospace, energy, and industrial applications.
If you require reliable mechanical property data or assistance designing parts for high-temperature service environments, our team is ready to assist.