Microstructure analysis is a critical part of materials science that focuses on examining and understanding the microstructure of materials. This includes their internal features, such as grains, phases, and particles on a microstructure level. This type of analysis provides insights into how the characteristics and arrangement of microscopic elements influence material behavior.
Why Use Microstructure Analysis?
There are several reasons to use microstructure analysis. First, understanding the microstructure is essential for predicting and optimizing the material’s mechanical, thermal, electrical, and chemical properties. It helps with quality control, finding defects or voids and making sure components meet performance standards.
It also shows how changes in conditions affect the microstructure. Environmental and process conditions, like temperature, pressure, and cooling rate, can all affect material behavior. In the case of material failure, analysis can figure out the root cause by looking at microstructural features like where cracks start, corrosion patterns, or changes.
What is Metallographic Analysis?
Metallographic analysis is closely related to microstructure analysis. However, it specifically focuses on the analysis of macro and microstructures for solid metals and alloys.
Through analysis, Secat can determine if your manufacturing process is under control. We compare clean samples with those that are out of specification, then interpret the data. This information will help you reduce the number of defects or optimize your process.
Moreover, because of our advanced interpretive metallographic capabilities, we can help you understand the relationship between microstructure and mechanical properties (with regard to product & process development). Additionally, we have access to some of the best metallographic tools in the world. Our unmatched independent expertise (particularly in aluminum metallography) can take your metal characterization to the next level.
Microscopy Tools and Techniques
Microscopy is a fundamental component of microstructure analysis for metals, allowing scientists and engineers to visually examine the structure and characteristics of metals and alloys at microscopic levels. This suite of microscopy and metallographic techniques uses various types of microscopes to magnify and analyze features that aren’t visible to the naked eye. From traditional optical microscopy to more advanced electron microscopy methods, each type provides unique insights into the material’s properties, microstructure, and composition.
Various Metallurgical Evaluations that Secat can perform:
- Macrostructure with etching
- Optical microstructure with grains
- SEM micrographs with particles
- SEM micrographs with phase and particle identifications using EDS and EBSD
- Weld microstructures
- Inverse segregation zone measurements
- Microstructures with defect identifications and size measurements
- Grain size measurements
- Particle size and fraction measurements
- PoDFA analysis
- Comparison analysis
Investigation Examples
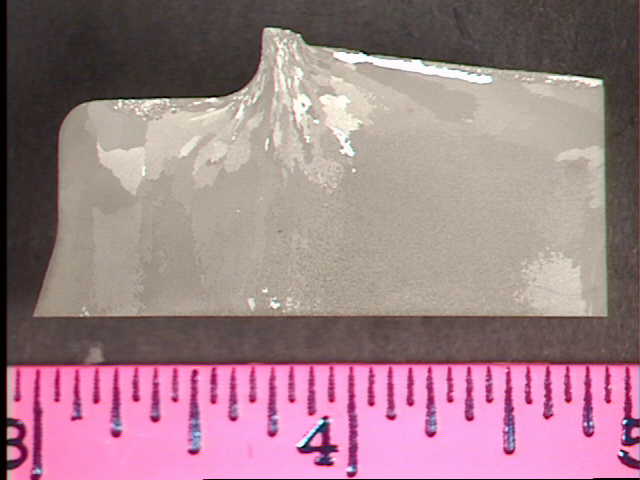
Macrostructure after coarse polishing and etching of forged product
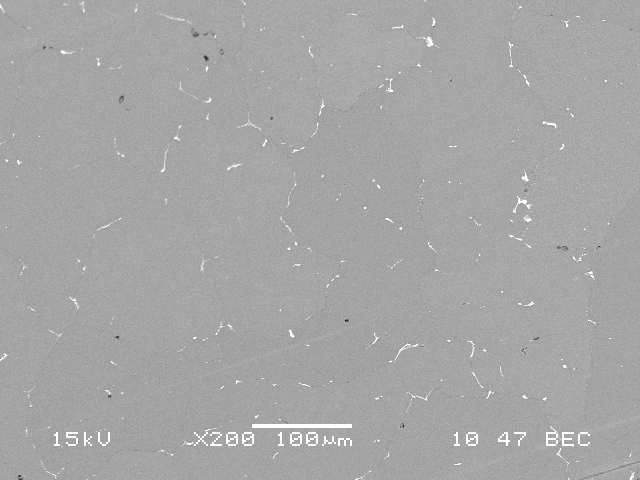
Particle structure in a billet
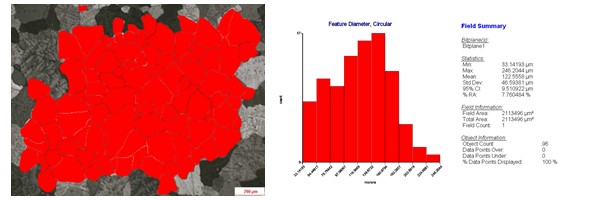
Grain Size evaluation using Omnimet software
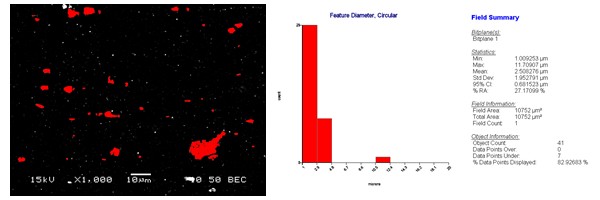
Particle size evaluation using Omnimet software