Customer Focus: Two critical variables to casting quality metals are inclusion content and hydrogen content. Inclusions can decrease the ductility, surface quality and fatigue strength in cast metal products (shape castings, billet or ingot) as well as their downstream product forms (rolled, extruded, forged or re-cast). Inclusions are essentially non-metallic materials (oxide films, carbides & refractory particles).
90% of all mechanical failures in metal products are due to dynamic stress fatigue failures. Fatigue cracks can initiate at inclusions during cyclic loading and can lead to crack propagation and ultimately failure of a component. Therefore, the measurement and control of inclusion content in molten metal is critical to maintaining good casting productivity and quality as well as the reduction of risk associated with product failure.
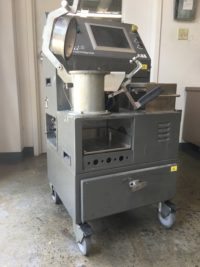
Prefil Footprinter® and PoDFA
To assess customer’s molten metal quality (composition and concentration of inclusions in molten metal) Secat utilizes the mobile PreFil inclusion analyzer. The PreFil is the only inclusion analyzer that provides an immediate result and, at the same time, creates a sample for further metallographic analysis. PreFil provides an immediate feedback on metal cleanliness from the metal flowrate through the filter. Because everything about the filtration is well controlled (pressure, metal temperature, …), the only parameter affecting the filtration speed is the inclusion content. One can determine the cleanliness level from the filtration curve (weight of metal filtered as a function of time). In addition to the filtration curve, metallographic analysis of the PreFil residue allows identification and quantification of the types of inclusions present in the metal sample. The build-up of inclusions at the filter surface during a PreFil test creates an inclusion band, which can be quantitatively analyzed using optical microscopy.
In addition to inclusion analysis, hydrogen content is also a critical variable in the production of cast metal products. Hydrogen gas porosity is an aluminum casting defect in the form of a void in caused by a high level of hydrogen gas (H2) dissolved in the aluminum at liquid phase. The solubility of hydrogen in solid aluminum is much smaller than in liquid aluminum. As the aluminum solidifies, some of the hydrogen comes out of solution and forms bubbles, creating porosity in the solid aluminum. Aluminum casting facilities want to produce high-quality aluminum castings with minimum porosity. Hydrogen porosity can be reduced by reducing through degassing the liquid metal. In wrought products (rolled, forged, extruded) small amount of porosity can be worked out. But in products produced with too much hydrogen, the resulting porosity can cause laminations and other defects in products. Further, hydrogen gas voids in shape castings can result in the initiation fatigue cracks in the end-product or if severe enough can cause a decrease in ductility.
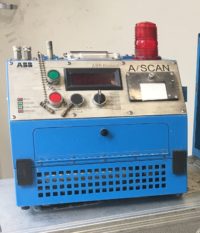
Alscan Unit
To monitor customer’s hydrogen content in molten metal, Secat utilizes the ALSCAN mobile hydrogen analyzer. The ALSCAN is a reliable quantitative technique to directly monitor the dissolved hydrogen content in liquid aluminum utilizing CLR. The Closed Loop Recirculation (CLR) is a proven method of directly monitoring hydrogen in molten aluminum. A small volume of carrier gas, usually nitrogen, is brought in contact with the melt by means of an immersed probe, and is continuously recirculated in the closed loop until its hydrogen content reaches equilibrium with the vapor pressure of H2 in the melt. The H2 concentration in the gas is measured and converted into a reading of the gas concentration in the metal. This method is fast, re-producible and accurate, and can be used “on-line” on the cast shop floor. The amount of H2 in the gas loop of the instrument is determined by a thermal conductivity sensor, which provides high reproducibility and a broad measurement range.
Whether your organization is aborting casts due to high inclusion content or experiencing high manufacturing rejection rates due to porosity, poor molten metal quality is extremely costly to your organization. Secat is happy to work with you to design a molten metal quality monitoring program that meets your company’s needs to ensure the best molten metal quality (lowest inclusion & hydrogen content) possible resulting highest quality and productivity!