Magnesium alloys are among the lightest structural metals and offer an attractive combination of properties, including good strength, stiffness, high damping capacity, and excellent thermal diffusivity. These characteristics make them ideal for lightweight applications in industries such as aerospace, automotive, and transportation. However, their broader adoption is limited by challenges such as high reactivity and poor corrosion resistance, which must be addressed for more widespread use.
Pure magnesium possesses a hexagonal close-packed (HCP) crystal structure and exhibits limited workability at room temperature due to restricted basal slip. At elevated temperatures, additional slip systems are activated, enabling improved deformation behavior. Alloying with elements such as aluminum and zinc encourages non-basal slip, enhancing workability. Minor additions of zirconium promote grain refinement in Mg-Zn and Mg-rare earth (RE) systems. Elements like lithium and indium can significantly improve workability by transforming the crystal structure from HCP to body-centered cubic (BCC). As a result, workability in magnesium alloys can be improved through alloying, grain refinement, or crystal structure modification—approaches widely used in alloy development for lightweight material solutions.
Challenges in Metallographic Preparation of Magnesium Alloys
Metallographic examination of magnesium alloys is commonly performed on polished and etched specimens for material characterization, quality control, failure analysis, and deformation process evaluation. However, magnesium and its alloys are among the most difficult metallic materials to prepare for microstructural examination. Their low hardness and strength make them prone to deformation during polishing, and the presence of hard precipitates complicates scratch removal and surface relief control due to height differences between phases.
Magnesium’s high reactivity raises questions about the use of water in the final preparation stages. Special care is required to avoid surface damage or corrosion during sample preparation. For clients seeking magnesium metallurgical testing, understanding these preparation challenges is key to achieving accurate and reliable microstructure analysis results.
Final Polishing Considerations for Magnesium Specimens
Final polishing is particularly challenging for magnesium and magnesium-aluminum alloy specimens. Alumina abrasives with particle sizes down to 0.05 μm are frequently used, typically suspended in aqueous solutions with soap, or in alcohol or ethylene glycol. While colloidal silica performs well for pure magnesium, it tends to etch magnesium alloys and is generally not recommended.
Water may be used for rinsing between grinding steps and after diamond polishing. However, it is usually avoided after final polishing, where alcohol or other non-aqueous solvents are preferred.
Mechanical Polishing Procedure for Magnesium Alloys
The table below outlines a standard mechanical polishing procedure used in professional metallography services for magnesium.
Mechanical Polishing Steps for Magnesium Alloys
Surface | Abrasive/Size | Load (lb/specimen) | Speed (rpm) | Time (min) |
SiC Paper | 120 grit, waterproof | 2–4 | 150 (Contra) | Until Planar |
SiC Paper | 240 grit, waterproof | 2–4 | 150 (Contra) | 2–4 |
SiC Paper | 400 grit, waterproof | 2–4 | 150 (Contra) | 3–5 |
SiC Paper | 600 grit, waterproof | 2–4 | 150 (Contra) | 3–5 |
SiC Paper | 1000 grit, waterproof | 2–4 | 150 (Contra) | 5–8 |
Trident PSA | 3 μm Diamond Suspension | 3–5 | 60 (Contra) | 5–9 |
ChemoMet Cloth | 0.05 μm MasterPrep Alumina | 3–5 | 60 (Contra) | 2–4 |
Note: In contra rotation, the platen and the specimen holder rotate in opposite directions.
Microstructure Analysis and Imaging
At Secat, Inc., we perform detailed microstructure analysis for magnesium alloys as part of our metallurgical testing services. The following images highlight typical results obtained through optical microscopy and scanning electron microscopy (SEM).
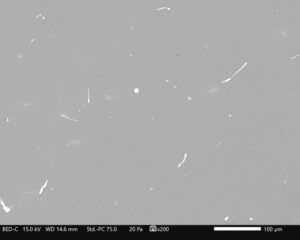
(x200) SEM image of Mg-Al alloy on the polished surface showing both MgAl phase and the MgAl+AlMn phases.
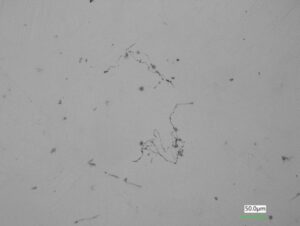
OM Image─ Optical photographs of the Mg oxide films in Mg-Al alloy
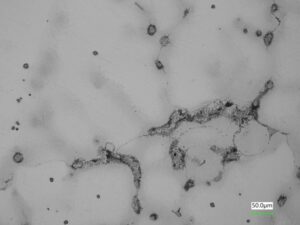
x500 – Optical microphotographs of microstructure after etching with Nital magnified.
Why Choose Secat for Magnesium Testing?
Secat is a leading metallographic testing lab in Kentucky, serving clients in aerospace, automotive, and manufacturing sectors. Our capabilities in failure analysis, aluminum and magnesium alloy testing, and lightweight materials evaluation are trusted by engineers and R&D teams nationwide. Whether you’re facing cracking issues in components or seeking expert insight into grain structure evaluation, Secat delivers reliable, high-quality results.
Interested in learning more? Contact us to discuss your magnesium metallography needs—from SEM imaging to corrosion testing and rolling process training.