SECAT Newsletter
Volume 12, Issue 1
July 2024 – Summer Issue
|
|
|
We are active on LinkedIn! Make sure you follow us!
|
|
|
|
Retirement
Dr. Chenghe Xiao – Technical Manager
After 23 years with Secat, we announce Dr. Chenghe Xiao’s retirement. Throughout his tenure, Dr. Xiao has been a pillar of expertise in casting, rolling, extrusion processing, and failure analysis of aluminum products. With his leadership in the lab and his commitment to excellence, Dr. Xiao is proud to have served hundreds of customers and driven thousands of successful projects. His dedication to lifelong learning will continue to inspire us all. Reflecting on his career, Dr. Xiao shares valuable advice for those aspiring to excel in this field: “Accumulate knowledge and experience. Do more and think more.”
As Dr. Xiao takes on this new chapter of retirement, he is looking forward to traveling, fishing, swimming and even taking piano lessons. We extend our gratitude to Dr. Xiao for his years of service with Secat. Congratulations, Dr. Xiao, on your well-deserved retirement!
|
|
Retirement
Janet Cecil – Office Manager
With Janet Cecil’s retirement, we said goodbye to a valued member of the Secat team. Since joining us in 2018 as an Administrative Support Associate, Janet’s diligent office administration was instrumental in keeping our everyday office operations running smoothly. Her warm and hospitable demeanor made an impression on all who visited our Lexington office. Janet managed information flow within our organization and effectively coordinated inbound and outbound shipments with our valued customers and suppliers. We extend our thanks to Janet and wish her all the best in her well-deserved retirement.
|
|
New Employee
Connor Varney – Post-Doctoral Associate
Introducing Connor Varney, the newest addition to the dynamic team at Secat, Inc.! With a bachelor’s degree in Materials Engineering from the University of Kentucky and ongoing pursuit of his doctoral dissertation, Connor brings an array of knowledge and enthusiasm to our organization. His current research focus is looking at the effects of part geometry and the resulting changes to the microstructure on the mechanical reliability of additively manufactured metal parts. Connor’s blend of academic rigor, practical experience, and a drive for innovation align perfectly with Secat’s mission of advancing materials engineering.
Connor’s journey into materials engineering was sparked by his life-long fascination with the automotive and aerospace industries. As an undergraduate, he led the mechanical engineering efforts for his university’s solar car team, resulting in the creation of a record-breaking vehicle. His transition to Ph.D. studies in 2019 was driven by a deep-seated curiosity about the transformative potential of metal additive manufacturing when he had the opportunity to work with GE on their metal additive manufacturing machines.
Beyond his academic pursuits, Connor’s passion for automotive engineering extends to competing in local autocross division. He is eager to leverage his expertise in alloys and collaborate with our team to tackle the diverse spectrum of research projects at Secat.
We’re excited to have Connor on the team!
|
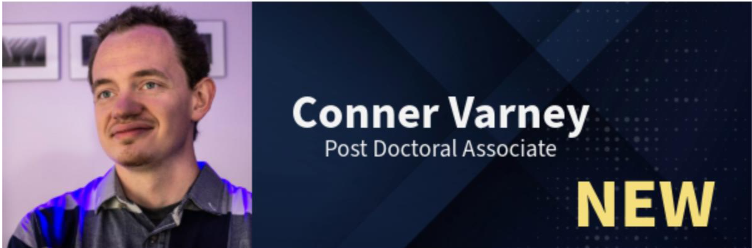 |
|
New Employee
Katie Myers – Sales & Marketing Manager
In late May 2024, we welcomed Katie Myers to our Secat team. In addition to the daily operations of office administration, she joins us as our new Sales and Marketing Manager at Secat, Inc. Katie holds both a bachelor’s degree of Media Communications and a bachelor’s degree of Communications, with a Public Relations emphasis from Asbury University.
Having lived in various regions across the United States, Katie brings wide-ranging perspective to her role. Her professional and personal journey together have fostered within her a genuine enthusiasm for cultivating, nurturing, and enhancing client relationships. With keen interest, Katie joins the Secat team, eager to immerse herself in the intricacies of our industry and champion our offerings through day-to-day office administration, brand representation and client relationships.
Welcome to Secat, Katie!
|
|
Molten Metal Splash Protection Testing
Fabric performance testing is essential for verifying PPE integrity in high-risk environments. Assessing durability, ensuring compliance, and confirming protective capabilities are critical. Secat offers molten metal splash protection testing, a valuable service for high-risk environments where safety is paramount – like melt shops.
Melt shops are among the most dangerous areas within a metal processing facility, posing some of the most demanding requirements for PPE used to protect workers. Garments worn by personnel must provide flame-retardant protection, be capable of shedding molten metal when splashed, and not deteriorate upon contact with the metal. Many facilities have developed “shop floor” tests to satisfy EHS department concerns. These tests typically involve attaching the garment to a wall, throwing a ladle full of molten metal at the garment, and then inspecting its condition afterward.
At Secat, we have developed a fixture suitable for controlled and systematic testing of fabrics exposed to molten metal, following ASTM F955 standards. The fixture consists of removable refractory plates, allowing for quick changeovers and eliminating the cool-down times required in a plant environment. A datalogger records the temperature at the copper calorimeters during the test. This temperature measurement allows for the calculation of the Stoll curve, a common method used to determine exposure time prior to a second-degree burn. The fixture stand holds a crucible with 1 kg of molten aluminum, which is poured in a continuous stream over the course of one second. This setup eliminates much of the variability inherent in shop floor tests, resulting in a repeatable and systematic test. Slow-motion video captures evidence of flame-ups and verifies that the pour occurs on the calorimeter.
After testing, Secat performs a visual rating of each fabric by examining the front and back. Each fabric is rated on performance criteria: ignition, adhesion, melting, embrittlement, break-open, charring, and shrinkage. Where applicable, a time to second-degree burn is calculated and reported, along with the maximum temperature for each calorimeter. Various fabric vendors and weights can be reliably compared, providing high-confidence judgments on the protection performance of each fabric and its suitability for personnel in the melt shop.
Below are pictures of the test stand, an example of a fabric tested, and the temperature/Stoll curve for the fabric. This fabric exhibited excessive adhesion of metal and did not shed the metal sufficiently. When the adhesion was removed, the fabric also showed charring and embrittlement with break-open in some areas. Adhesion, embrittlement, and break-open of the fabric are all criteria that could potentially result in injury to a worker exposed in such a manner. The maximum temperature recorded during the test was 185°F, and the top calorimeter exceeded the Stoll curve just 0.2 seconds into the testing, which is expected to result in a second-degree blister burn.
|
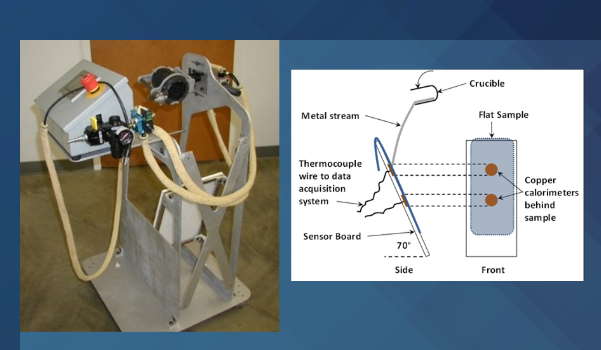 |
|
Additionally, Secat has developed a test fixture, designed by a senior team from the University of Kentucky, for testing boots exposed to molten aluminum. The boot is lowered into molten aluminum at a specified temperature, held for a set time, and then removed. Calorimeters inside the boots and a refractory backing ensure the heat is absorbed by the calorimeters to determine maximum temperatures at different points within the boot.
|
|
Enhance your fabric reliability with Secat’s molten metal splash testing. Our systematic approach provides comprehensive data on protective gear and fabric performance. Contact us to learn how our testing services can benefit your facility.
|
|
Tech Talk
Development of a High Strength Corrosion Resistant AA6XXX Alloy
Over the past two years Secat has undertaken work on an internal alloy development program. The program objective was to develop a new AA6XXX alloy with higher strength compared to existing alloys and good corrosion resistance for use in automotive and aerospace applications. Thermodynamic modeling (ThermoCalc) was used to identify promising experimental alloy chemistries based on intermetallic phase equilibria. A copper book mold was designed and manufactured, and ten candidate alloys were initially cast at the University of Kentucky. After initial testing, five more alloys were cast at Secat. After casting, the ingots were homogenized, hot rolled, solution heat treated, and aged to final temper. The microstructures of the samples were evaluated, and specimens were prepared for tensile, hot compression, and corrosion testing. The particle structure and microstructural evolution of the alloys were characterized at different steps of the manufacturing process by use of Scanning Electron Microscopy (SEM) with Energy Dispersive Spectroscopy (EDS) and Optical Microscopy. Representative images of the particle and grain structure (EBSD) taken on Secats new Joel FE-SEM with Oxford EBSD detector are shown below.
|
|
The strength of the candidate alloys was evaluated by tensile testing of subsized (1 in) gauge length flat samples that were machined and then tested on a servo-hydraulic MTS 810 testing system in strain control. The plot below demonstrates clear improvements in strength compared to the baseline alloy composition.
|
|
Corrosion resistance was determined by performing an acetic acid-salt spray (CASS) test according to ASTM B368 in Secat’s Q-Fog test chamber. The samples were exposed for 24 hrs and were then evaluated for pitting and intergranular corrosion. An image of the corrosion on one of the samples after testing is shown below.
|
|
The amount and severity of pitting on the sample surface was measured by use of Secat’s Keyence Digital Microscope. The data showed that the new alloys performed as well or better than the baseline with respect to resistance to intergranular corrosion.
Hot compression testing was also performed by use of Secat’s MTS 810 servohydraulic test system. Flow stress measurements from compression tests relate directly to the force required to initiate and maintain deformation processing by rolling, forging or extruding of a billet. The curves obtained at 900°F are presented below. The flow of the modified alloys are higher than a common extrusion alloy, AA6005 but close to the flow stress for the baseline AA6099 alloy.
|
|
Secat is planning to schedule a full scale, 10 inch diameter billet cast of the new alloy chemistry in 2024 and is seeking collaboration with extruding and/or forging companies for demonstration.
|
|
Visit us at www.secat.net and check out all that we have to offer!
|
|
Aluminum Art
Gotta LOVE Aluminum
Robert Love has spent over thirty years in Art education, teaching all grade levels from kindergarten to college. He was the art teacher at the School for Creative and Performing Arts (SCAPA) in Lexington, Kentucky for twenty-five years. As a Kentucky Crafted artist, Robert creates mosaic-style art from recycled aluminum cans, calling it “Recycled Brushstrokes “. He received his master’s in Art Education from Western Kentucky University. Robert’s art has been displayed all over Kentucky and is in the collection of the Coca-Cola Museum.
Watch for his work coming soon to the Kentucky Artisan Center in Berea, KY.
Contact loveartbg@gmail.com for more information
|
|
Do you have a piece of Aluminum Art you’d like to share? Contact us at info@secat.net
|
|
Don’t Forget to Connect with Secat on Social Media!
|
|
|
|
|